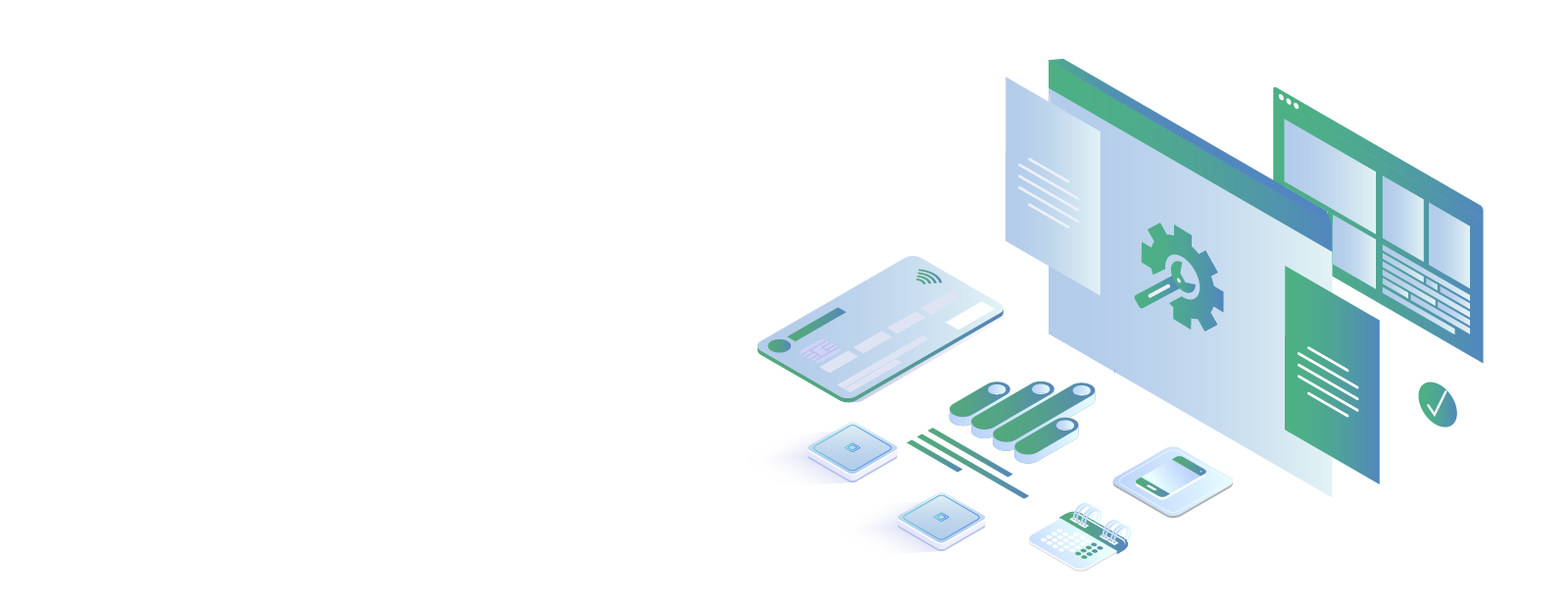
Visual Quality Inspection
Retail & CPGBusiness Impacts
99.4%
Model accuracy
100%
Coverage
Customer Key Facts
- Location : Europe
- Industry : Food & Beverages
Problem Context
The client is the world’s largest multinational drink and brewing holdings company based in Belgium. In their manufacturing plant, cartons on a high-speed conveyor belt were manually inspected by employees every 15 minutes for damages, such as dents in packaging, errors in barcodes, and other defects. If damages are found, then the conveyor belt is stopped and necessary tweaks need to be made.
In the event of a damaged package escaping the employees check, the client bears all costs involved in shipping the package back from the customer’s location and sending a new one. The client, therefore, wanted to reduce the number of manual errors in the quality control process before any product is shipped.
Challenges
- Variety of products and packages ( i.e. bottles/cans/cartons)
- Total of 22+ QC checks to be done for products
- High-speed motion of conveyor belts
- Generation of data from videos
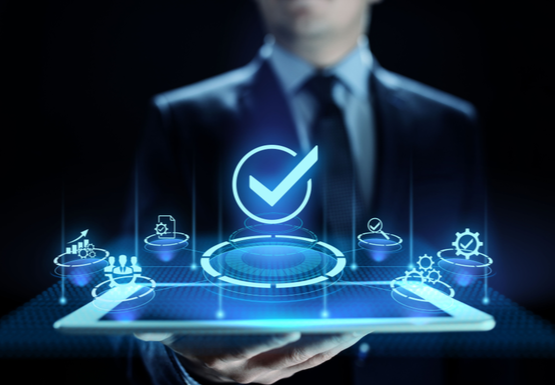
Google Cloud Platform
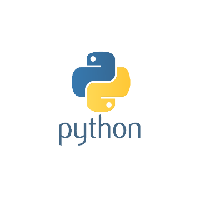
Python
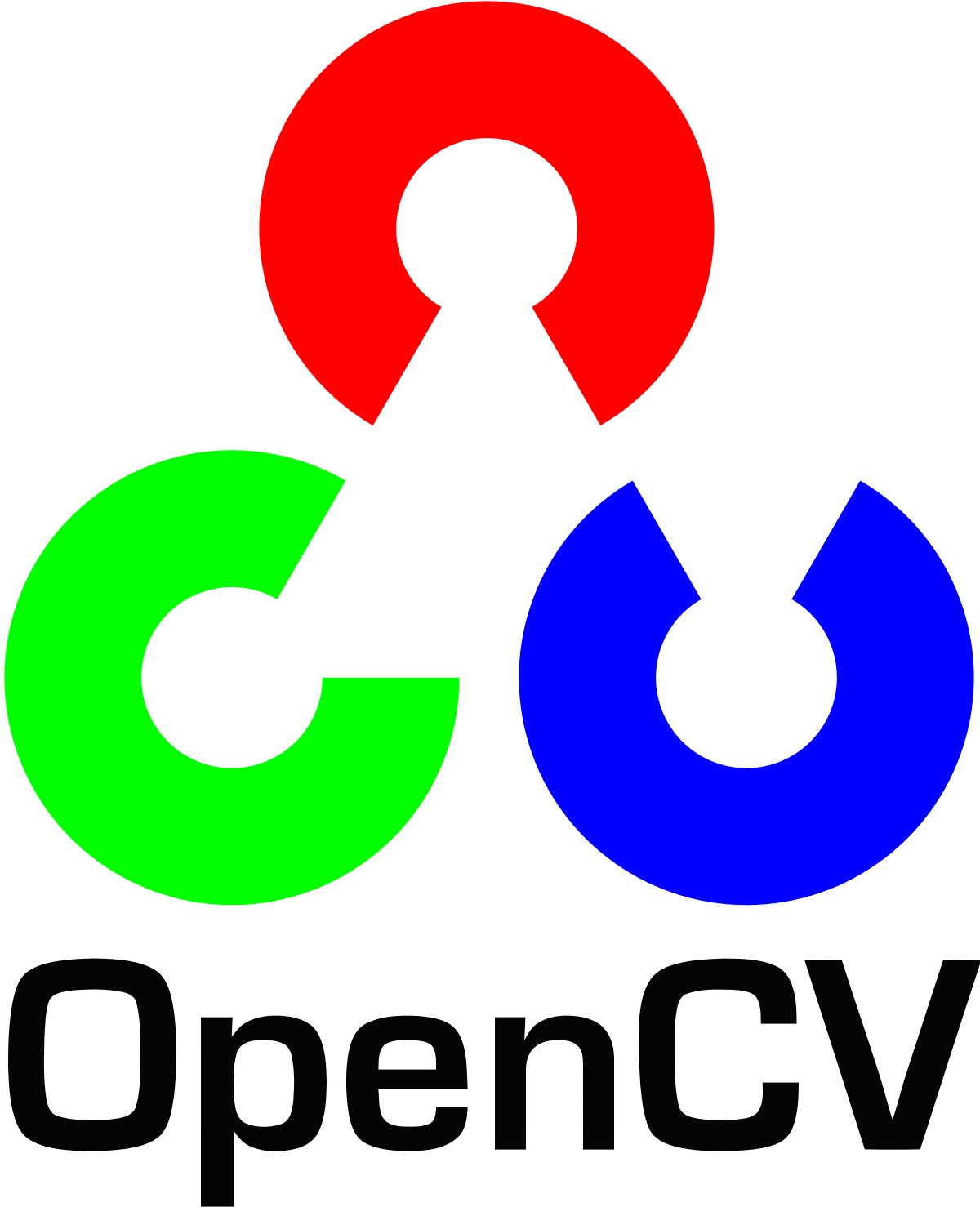
OpenCV
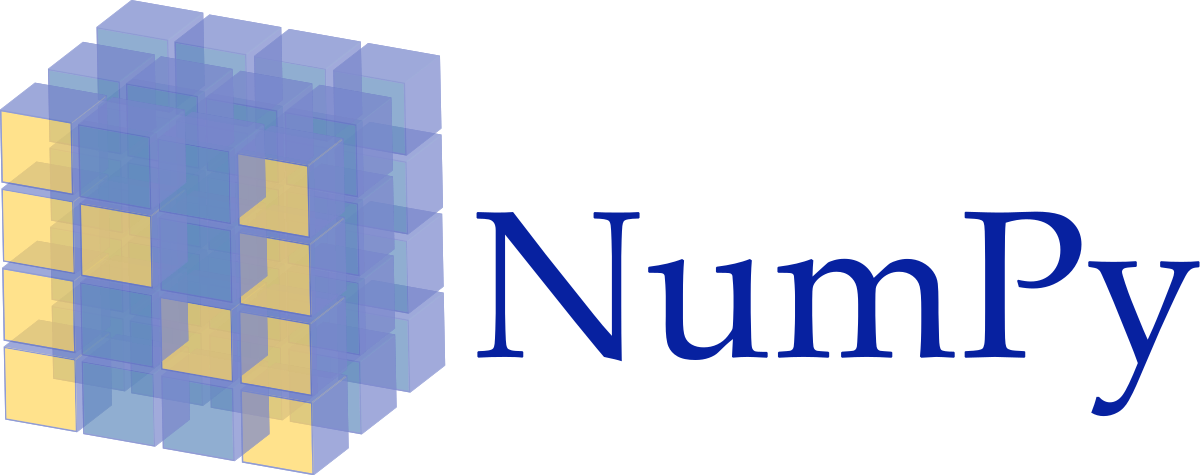
NumPy
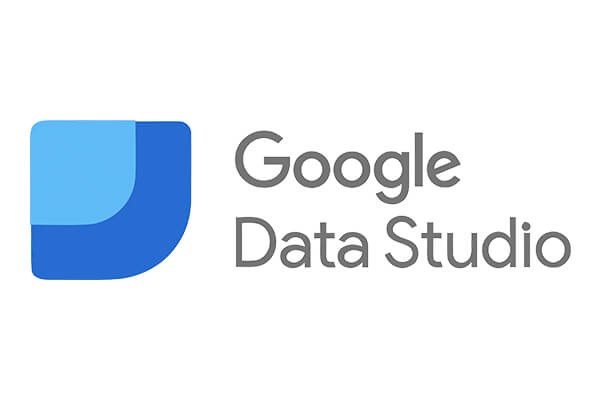
Google Data Studio
Automating the Quality Check Process for Detecting Barcode Errors on a High-Speed Conveyor Belt
Solution
Quantiphi developed a custom computer vision model that automates the quality control process by accurately detecting errors in the barcode while a product is moving at high speeds on the conveyor belt. This framework also automates the inspection procedure for different types of packages, including quality checks for dimensions, graphics and other defects.
Result
- Faster inspection process
- Reduced manual efforts
- Greater cost savings