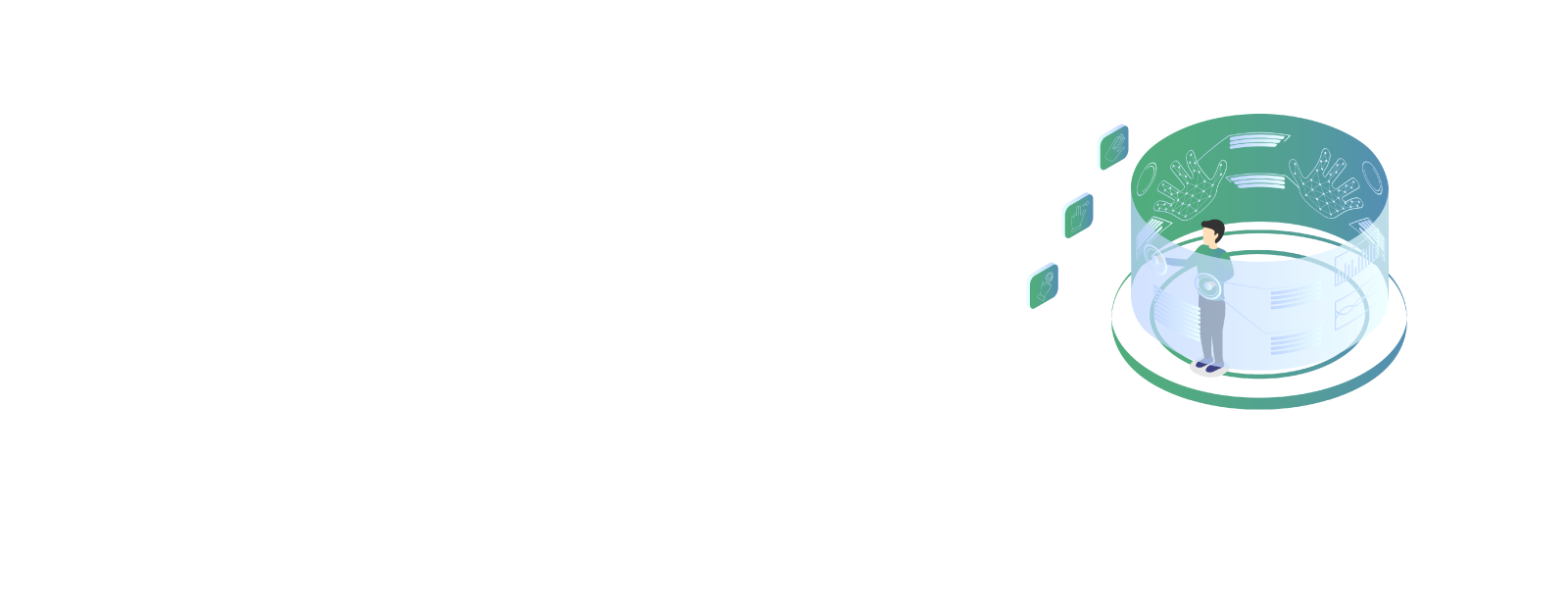
Virtual Screening of Material Design
ManufacturingBusiness Impacts
94%
Model accuracy
12 Hours
Saved per test
$2 Million
In potential annual savings
Customer Key Facts
- Location : North America
- Industry : Manufacturing
Project Context
The customer, a leading global manufacturer, designs world-class critical safety systems including brake pads and shock absorption technology for automotive firms around the world. The material scientists and chemical formulators use their domain knowledge and experience to formulate chemical compositions to design the brake pads with friction coefficients specific to the automobile requirements.
Their Research & Development team invests significant time and money to test and determine friction performance levels of the brake pad material. Therefore, this is a complex process that requires a great deal of testing and engineering.
They wanted to implement an automated solution to predict the friction coefficient and material coefficient of a brake pad in order to reduce the number of iterations in designing a brakepad while also reducing the resources wasted in testing.
Challenges
- Fewer data points to train the model
- Sparse and high-dimensional datasets
- Large number (2000+) of input features
- Alignment of feature importance to business understanding
- Complex and unstructured data collected over 20 years
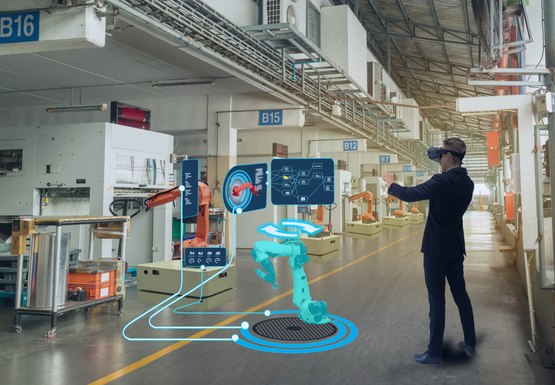
Technolgies
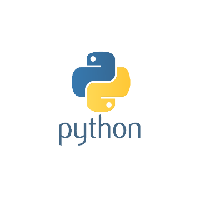
Python
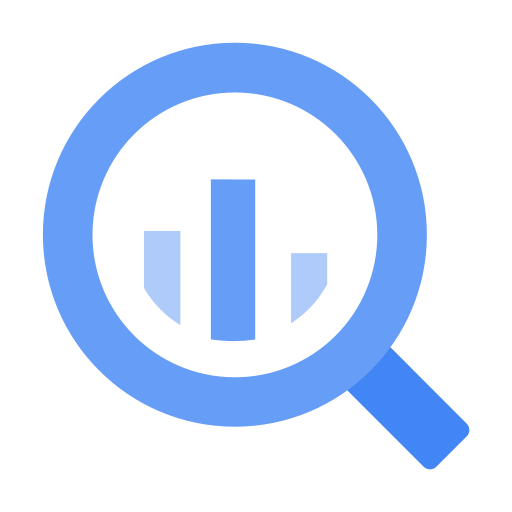
Google's BigQuery
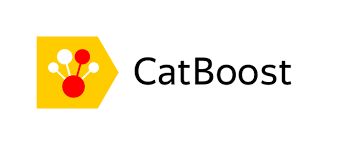
CatBoost
Google Cloud Platform
Determining Key Factors Affecting Friction Characteristics and Assisting in Brake Pad Friction Material Design
Solution
Quantiphi developed a simulation environment with a virtual material testing framework to conduct the tests live without wasting too many resources. The virtual testing solution enables chemical formulators to design materials on the desktop and run confirmatory tests only for the most promising material compositions; allowing preemptive screening of sub optimal brake pads and identification of optimal designs.
Quantiphi also developed a web-based user interface for predicting the friction coefficient of the brake pad enabling chemical formulators to submit input features and get corresponding friction coefficient of the designed materials.
Result
- Lower formulation and testing costs
- Reduction of the resources wasted in testing
- User can view output in graphical & tabular format